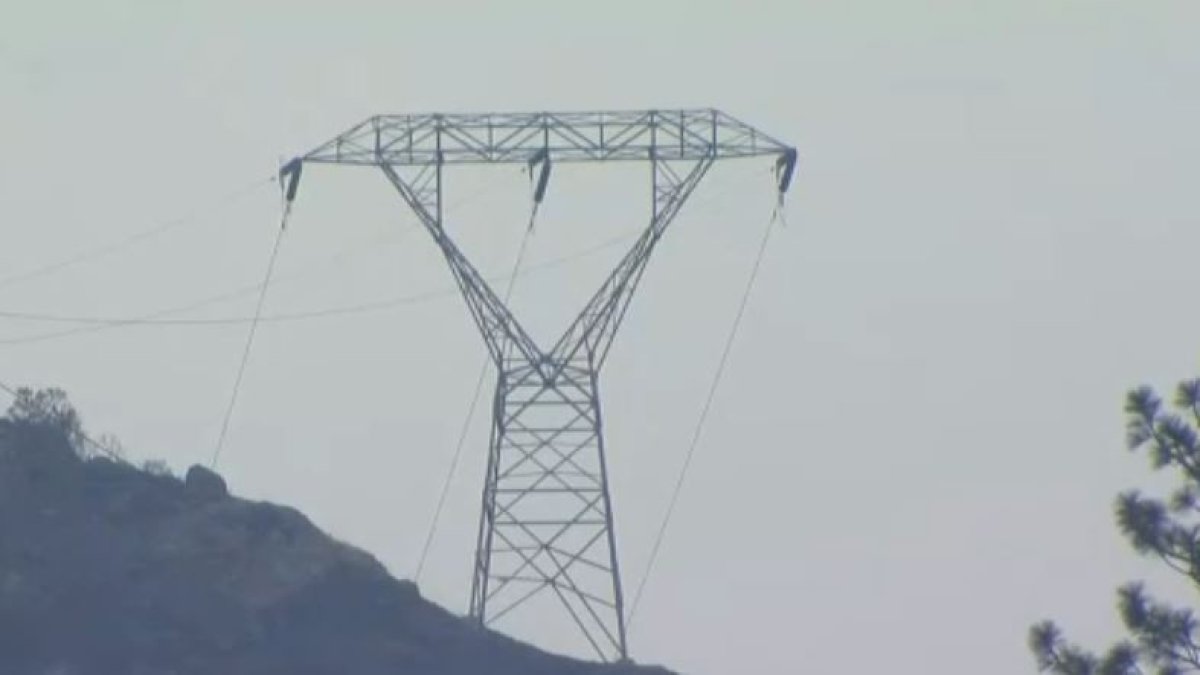
In a recent report, California regulators say a small fire revealed "flaws of PG&E’s maintenance program and its failure to provide safe and reliable service" amid the utility's massive repair backlog in high-fire-risk areas.
In response, PG&E released the following lengthy statement:
PG&E’s proven layers of protection have significantly reduced wildfire risk from our equipment. Since we launched our Community Wildfire Safety Program, we have mitigated ~90% of wildfire risk caused as a result of our equipment and are on track to mitigate 94% of the risk in 2023. (Based on the methodology established by the California Public Utilities Commission in the Safety Model Assessment Proceeding and implemented by PG&E, accordingly.)
Our efforts include:
Get a weekly recap of the latest San Francisco Bay Area housing news. Sign up for NBC Bay Area’s Housing Deconstructed newsletter.
- Our 10,000-mile Undergrounding Program is the largest known effort in the U.S. to underground powerlines as a wildfire risk reduction measure.
- In addition to undergrounding, we are strengthening the electric system with stronger poles and covered powerlines within high fire-risk areas.
- We are managing trees and other vegetation located near powerlines that could cause a power outage and/or ignition.
- We continue to reduce the impact of Public Safety Power Shutoffs (PSPS). While there were no weather-driven PSPS outages in 2022 due to favorable wind conditions, it continues to be a top focus for our team.
Another layer of protection, Enhanced Powerline Safety Settings (EPSS), has significantly reduced ignitions and further mitigated wildfire risk for our customers living in high fire-risk areas. This measure of protection is a proven wildfire mitigation tool. In 2022, we achieved a more than 68% reduction in CPUC-reportable ignitions on EPSS-enabled lines in High Fire-Threat Districts (HFTDs) compared to the 2018-2020 average. And, if ignitions did occur, the size of fires were much smaller thanks to EPSS.
As detailed in our 2023-2025 Wildfire Mitigation Plan (WMP), we continue to aggressively work to reduce our inventory of maintenance tags, always prioritizing on finding and fixing items that could pose an immediate safety issue.
Local
Since 2019, PG&E has significantly increased the frequency and methods of our inspection programs. In comparison to the five-year baseline required by General Order 165, assets in high wildfire risk areas are inspected at least once every three years, and more frequently (annually or every two years) based on wildfire risk. In addition to patrol and ground inspections, PG&E also has implemented additional methods such as drone/aerial inspections for more comprehensive view of the asset condition. Lastly, the inspection checklist used by inspectors was built with a high level of specificity at the component level to ensure a detailed and complete assessment. This significantly enhanced inspection protocol has resulted in three to four times the number of tags which are mitigated through risk-informed prioritization.
In our 2023-2025 WMP, we provided targets for addressing repairs found during inspections, prioritizing work with the highest potential ignition risk within the High Fire-Risk Areas (HFRAs). We have developed a plan to reduce the wildfire risk associated with these open ignition-risk tags in HFRAs by 77% at the end of the 2023-2025 WMP cycle.
In relation to the Brewer Fire incident and associated CPUC citation, we don’t dispute the facts as outlined by the CPUC. A 5-acre fire occurred on July 7, 2021, in Grass Valley. No structures were damaged, and no injuries were reported. Cal Fire determined that a heated piece of metal from PG&E’s electrical equipment likely fell into the dry grass below and started the fire. PG&E had seen a potential issue prior to the incident based on an infrared inspection, but the repair work was delayed after a physical inspection by a PG&E inspector.
The incident didn’t meet the threshold for filing an Electric Incident Report (EIR) until Dec. 22, 2021, when a claim for property damage exceeding $50,000 was received by PG&E. PG&E filed an EIR on this incident the next day, Dec. 23, 2021.
The CPUC’s Safety Enforcement Division (SED) determined that PG&E had six violations of GO 95 rules ranging from one day to 592 days. In issuing its citation, which came with a penalty of $132,500, the agency cited aggravating factors, including three similar previous violations, as well as mitigating factors such as PG&E’s cooperation throughout the investigation and the corrective actions that PG&E identified in our Event Analysis Report as well as in the supplemental 20-day EIR report. PG&E does not dispute the citations and paid the penalty on June 6, 2023.
These corrective actions include:
- Electric Corrective (EC) tags that originated from Pole Test & Treat (PT&T) or infrared (IR) inspections are not eligible for the Field Safety Reassessment (FSR) process and are therefore not to be included in the FSR list.
- Tailboard meetings have been held with relevant personnel to reject cancellation requests from FSRs related to IR or PT&T.
- Previously canceled EC Tags initiated by an IR inspection were reopened if the cancelation was initiated after a visual-only inspection or if the maintenance history suggests the incident equipment identified by IR has not been replaced. This process has been completed.
- A procedure for FSRs is being updated that establishes a built-in Quality Control (QC) check as an extra layer of review. Updates also will be added to the Electric Distribution Preventative Maintenance Manual and tracked in the corrective action program.
I wanted to share a few definitions as well:
- Electric Corrective (EC) notifications track emergency and planned maintenance work on PG&E's distribution lines. EC tags account for all levels of priority (A, B, E, F, etc.).
- We use Field Safety Reassessments (FSRs) as an internal containment activity to mitigate potential safety issues on lower priority E and F tags. FSRs are where we re-review these lower priority tags that may not be completed within the tag’s associated prioritization to ensure that the situation has not worsened. If it has, then that tag gets elevated to a higher priority for repair.
- FSRs are not the only containment activity for re-reviewing existing tags. Tag Validations are performed during regular Inspection efforts. Any outstanding EC Notification is reviewed by our inspectors during their regular inspections to determine if the condition still exists -- sometimes the condition is corrected as part of another incident or emergency without the EC Tag being closed -- or to identify if the Electrical Corrective condition has worsened and needs to be elevated to a higher priority.